

- #Woodpecker 3.2 grbl documentation mod#
- #Woodpecker 3.2 grbl documentation drivers#
- #Woodpecker 3.2 grbl documentation driver#
- #Woodpecker 3.2 grbl documentation upgrade#
- #Woodpecker 3.2 grbl documentation full#
Arduino-ide did not detect the board automatically but the flashing to grbl 1.1h worked with a following command out of the box on my linux by using a following avrdude command: avrdude -v -C/etc/avrdude/nf -pm328p -carduino -P /dev/ttyUSB0 -D -Uflash:w:grbl_v1.1h.20190825.hex
#Woodpecker 3.2 grbl documentation upgrade#
Original GRBL firmware was 0.9j but I managed to upgrade it to v1.1h over USP without need for using another arduino as a ISP programmer and wiring it to woodpecker. I have not yet tried to workflow from Kicad, to flatcam and from there to bCNC. In the meantime I have not constructed my CNC 2418 from Jack's store and tested that I can control it by seding the g-gode commands from terminal. This might be a bit small if you wanted to make a complete cover made out of this stuff Thanks for the shielding material tip, I may buy it later if starting to work with 0.5w 405nm laser for engraving. It is rated for the wavelength of my laser module which is 450nm. I got a piece of this to replace the plexiglass on the door of my enclosure. One of the tools is a 6 watt laser module.
#Woodpecker 3.2 grbl documentation mod#
Not long ago I made a mod for my 3D printer that allows me to change to different tool heads. I made an enclosure for my 3D printer in which I had a plexiglass panel for the door.

#Woodpecker 3.2 grbl documentation full#
I have only found out so classes for protecting from the beam but would rather like to see a full box made from proper shielding material on top of the Eleksmaker.įourths interesting thing is the openpnp based pasta dispenser and pick and place machine. Laser is interesting due to it's accuracy but I am worried from the reflected beams. I'll be plugging them into a RAMPS board, which is cheap, and which, as an arduino Mega 2560 shield, will replace the woodpecker said in CNC PCB milling: I got a couple extra in case I accidentally burn one or two of them out.
#Woodpecker 3.2 grbl documentation drivers#
The yet to be used trinamic drivers cost $42.50: Not sure yet whether the new spindle will eventually produce better results or not, although it does run quieter, which is nice. My feeling is that the steel rods are a worthwhile and very easy upgrade, even though I don't have data to prove they make any difference. The 6 chromed steel smooth rods cost around $20-30 in total, including e-packet delivery. Aside from the plastic filament needed for the print (maybe $2 worth), it requires just 4 short linear bearings and a lead nut. I had to 3D print an adapter for the new spindle to fit onto the 2418. I power it with a separate, adjustable power supply, since it can go to 48v. The spindle I'm currently using cost $34: What was the cost for the overall upgrade? Or, just get this, which goes to 24,000RPM and has water cooling already a part of said in CNC PCB milling: The main downside to that is that it would require installing an ER11 collet, and so runout might be an issue. It could also go up to around 48,000RPM at 12v. Notionally, something like: Īlternately, I notice an inexpensive brushless motor with a water cooling jacket already installed, for not much money: In addition, the user will be optically shielded from light exposure.Perhaps it would be possible to buy a water cooling jacket for the spindle? That would cover the bases against even heavy duty use. I plan to have a Laser Enable Switch, interlocks, and flashing strobe light added to my system that is in the 12V circuit.

I have already seen one case where VigoWorks left the laser on when it crashed.Īlso when enabled there should be a clear indication that the system is UNSAFE. I don’t like conditions where the laser can be on without you knowing or deliberately enabling it.
#Woodpecker 3.2 grbl documentation driver#
Lack of manual control of the laser’s power also assumes that the driver software will never activate nor leave a job running without you asserting or knowing it has been left on.
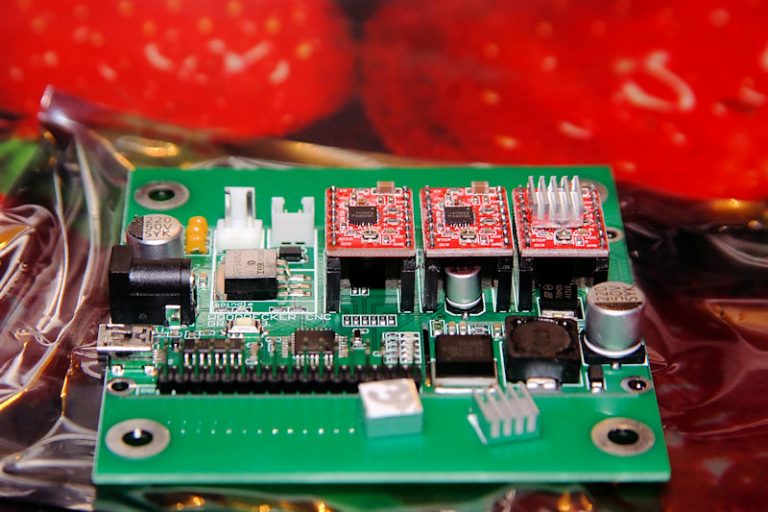
Although it should, I would not trust the controller to hold PWM at 0 during POR. I would not assume the PWM asserts to 0 before the 12V comes up. Experience has taught me not to trust software and hardware design where I cannot see code and schematics for myself. In systems designed for laser safety, I do not trust my eyes to software and electronics. Thinking about the issue of the laser coming on at power-up…isn’t it the case that pwm=0v means the laser will be off (yes, the fan will spin up, but it won’t actually lase until pwm>0v) ?
